ALUMINA COMPONENTS UK
UK & Europe wide.
We cater to the Alumina components UK market offering a wide range of precision engineered ceramic alumina components across the UK and mainland Europe. Advanced Ceramic Engineering’s alumina raw material is processed with certain additives, spray-dried and cone blended under strict quality control, then allocated to a batch number to ensure traceability throughout the manufacturing process. We recognise that no single alumina composition can fully meet every single technical requirement. Therefore we offer six grades which range from vacuum tight to porous alumina. Any of these can be tailored to meet individual design requirements exactly.
Vacuum tight materials
The ACE500, ACE600 and ACE300 materials consist of fine grained alpha alumina crystals bonded with various percentages of high temperature alkaline aluminosilicate glasses. The ACE995 material is an extremely high purity (99.5 % alumina), sintered aluimina with a very low glass content. The ACE995 T1 fine grained has the highest of purity and the smallest grain size of all the materials. It offers enhanced surface finish and resistance to chemical attack. All ACE bodies have particularly low neutron absorbtion cross-sections. As a group, the vacuum tight bodies feature very high strength and abrasion resistance, permanent stability, high thermal conductivity, chemical inertness, and exceptional electrical properties at room and elevated temperatures.
Porous materials
The porous ACE-1009 has a very high purity, re-crystallised alumina composition. This material is completely free of any reducible impurities, and has an extremely high melting point ( 2000 degrees C), and high reflectivity. Because of these properties ACE-1009 is widely used for cathode heater insulators in vacuum tubes, and for solid state laser cavities.
Mechanical strength
Compared with most insulating materials, the ACE alumina bodies have a greatly superior tensile, compressive and cross-breaking strength. They are at least twice as strong as conventional electrical porcelain. These high mechanical strength properties are unaffected by relatively high temperatures.
Thermal conductivity
The thermal conductivity of all ACE bodies is far greater than that of conventional ceramic materials and glasses. For example, the thermal conductivity of ACE300 (26.8 Wmk) is ten times that of steatite ceramics, and 20 times that of borosilicate glass. Heat is therefore rapidly dissipated through the material.
Electrical Reistivity
All ACE aluminas have extremely high electrical resistivity at both room and elevated temperatures.
Chemical inertness
ACE aluminas – especially the ACE995 & ACE995 T1 posses a high degree of chemical inertness which ensures against product contamination. They are also resistant to attack by most chemical and corrosive materials, whether in solid, liquid or gaseous form.
Hardness and abrasion
The hardness of the ACE bodies (Rockwell 45N) is comparable to that of Sapphire, and uniform in all batches of any particular grade of material, since these are produced to a specific gravity (depending on the material requested) of between 3.67 for ACE500 and 3.90 for ACE995 T1. Because this hardness is scarcely affected by temperature, a high resistance to abrasion is ensured over a wide range of service conditions.
Optical reflectivity
The ACE1009 body, when glazed, has a reflectivity in excess of 95% of incident light over various wavelengths. This makes it highly suitable for use in solid state laser cavities.
Irradiation
As well as possessing the above properties, the ACE bodies remain stable under conditions of irradiation, which makes them suitable for use with most other materials utilised in reactors.
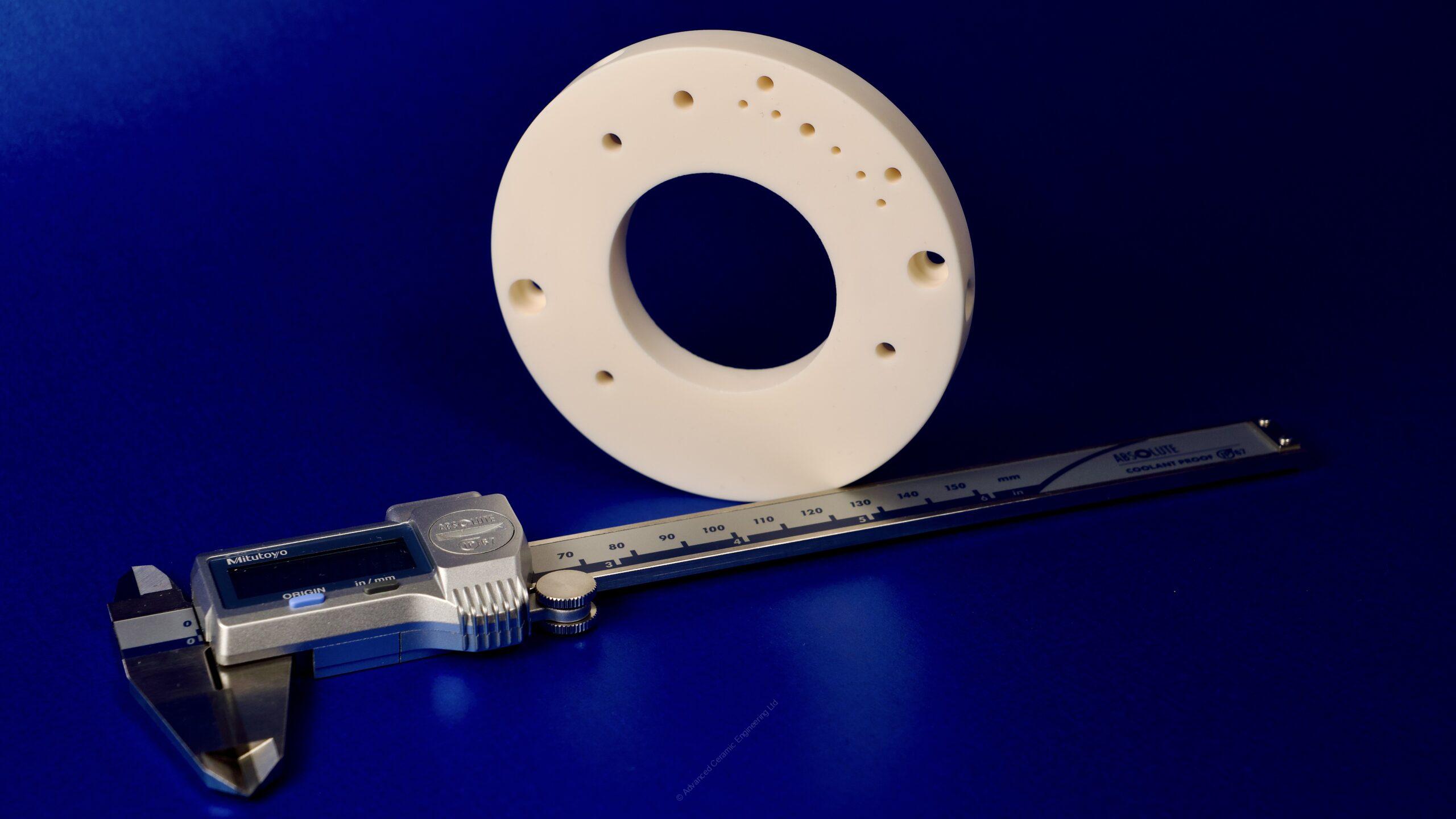
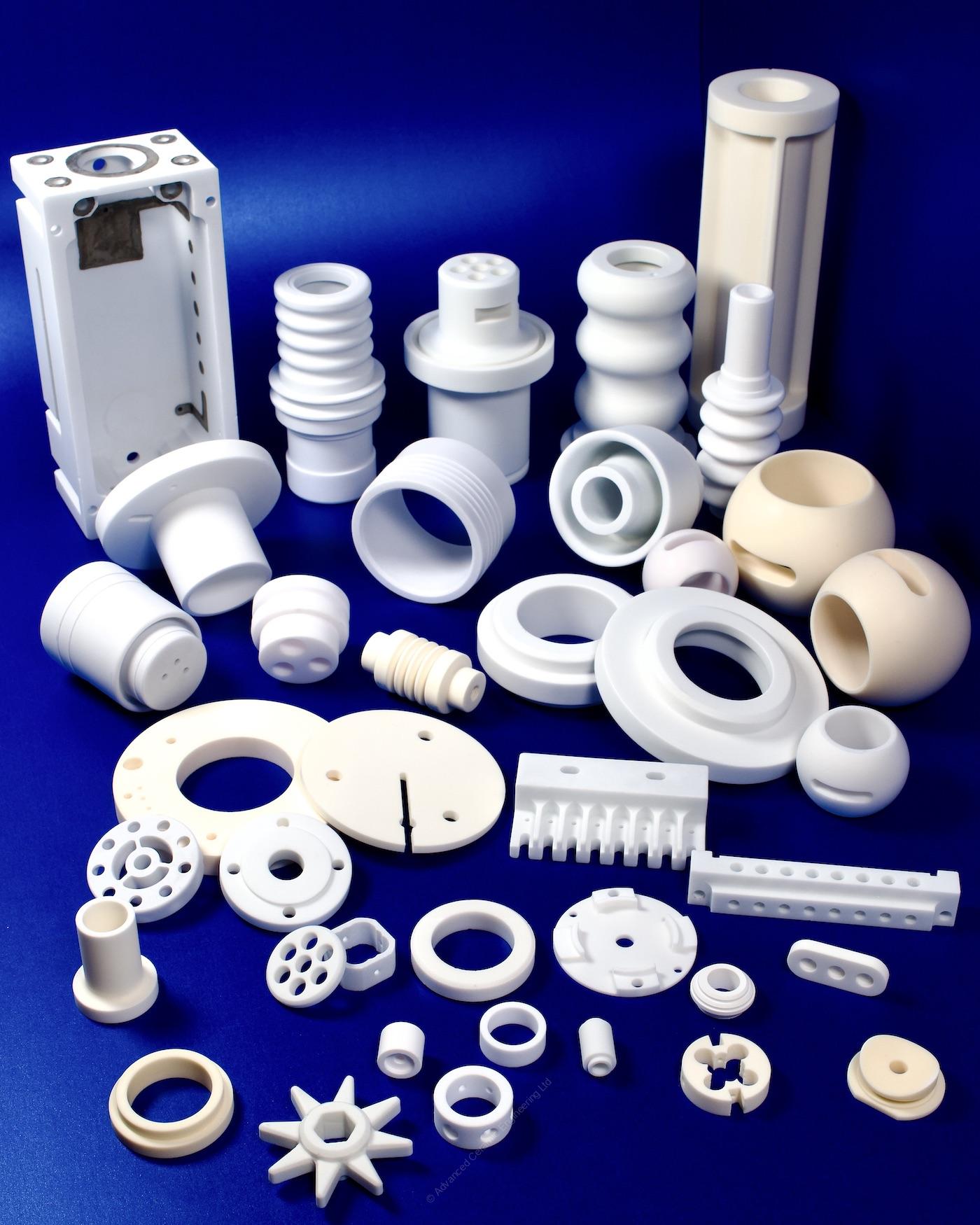
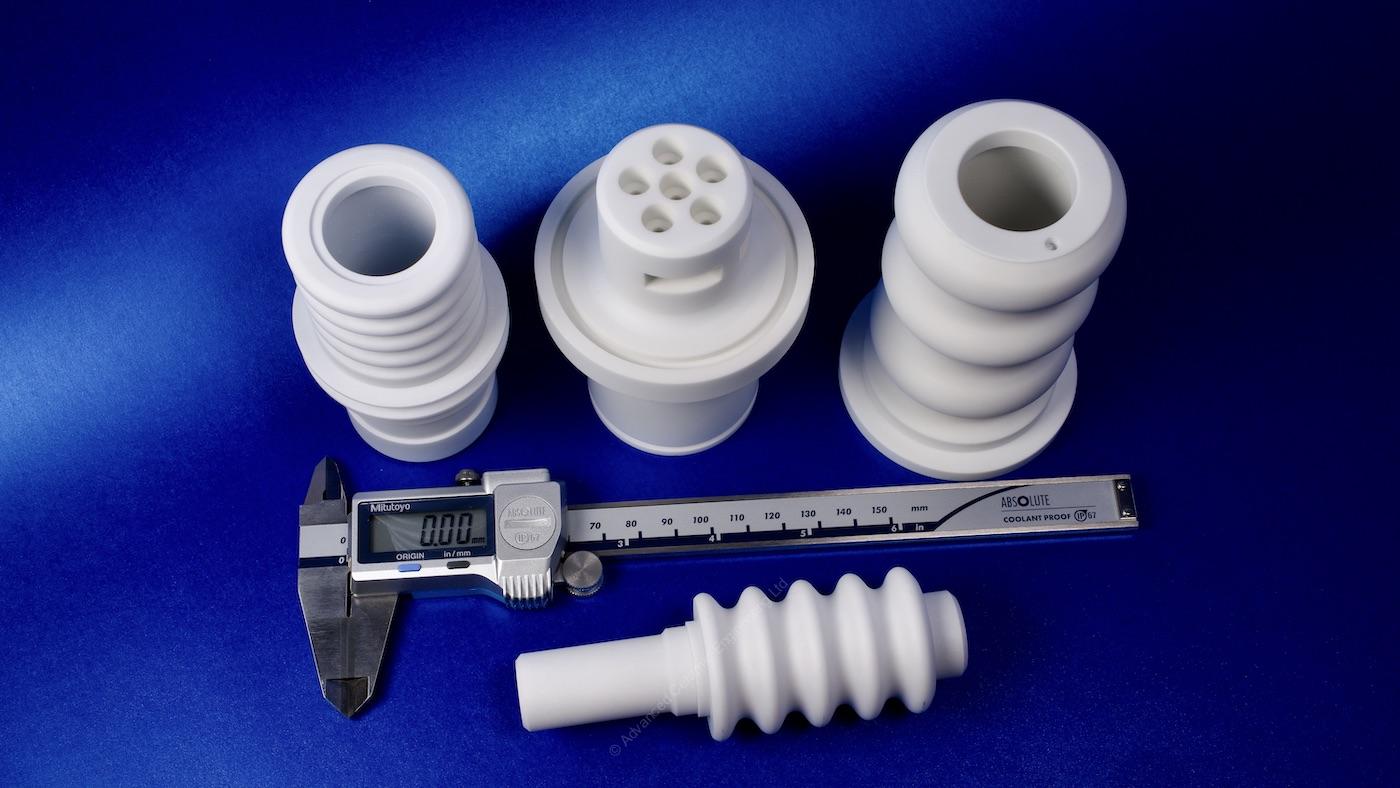
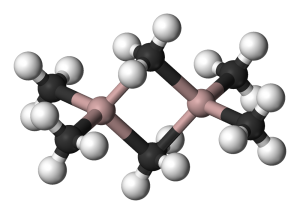
- We supply UK & Europe wide
- 40 Years Experience
- Wide range of solutions